The path to smarter financial decisions begins with a precise understanding of the *total cost of ownership* (TCO). Downloading a TCO calculator provides an invaluable resource for anyone seeking to make informed purchasing decisions, whether for personal or business purposes. Leverage this tool to dissect the complex layers of costs associated with any asset, going beyond the initial price tag to include hidden expenses like maintenance, operation, and eventual disposal costs.
Initiate the process by downloading the TCO calculator from a trusted source, ensuring it meets all your specific requirements. Once downloaded, the next step is straightforward. Input all relevant data, such as purchase price, projected maintenance costs, and estimated lifespan. Utilize the intuitive interface that many modern TCO calculators offer, allowing for easy data entry and instant results. This step helps highlight areas where you might optimize savings, enhancing your overall financial strategy.
While navigating this tool, it’s beneficial to follow a tutorial that provides a step-by-step guide on maximizing its potential. Such tutorials often illustrate common scenarios where a TCO calculator becomes indispensable. They reveal how to accurately project future costs and make comparisons between different purchase options. Harness these insights to explore scenarios like buying versus leasing, energy-efficient options versus standard models, and other similar analyses that can significantly impact your financial planning.
Comprehensive Overview of TCO Calculators
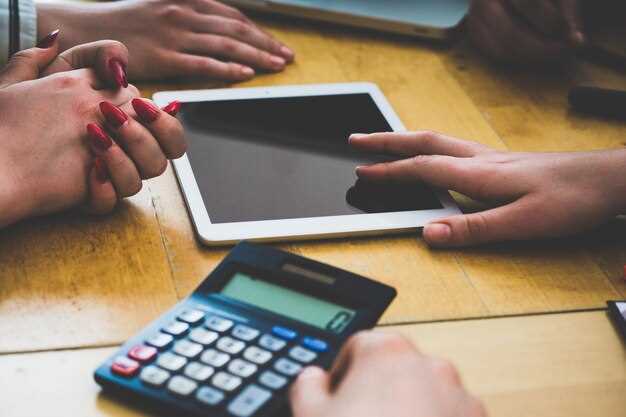
Begin by identifying the key components that impact the Total Cost of Ownership (TCO). This includes initial costs, operational expenses, maintenance, and end-of-life costs. An effective TCO calculator provides a clear breakdown of these components, allowing you to make informed financial decisions.
A valuable TCO calculator should offer customized input fields so you can input specific data related to labor, energy, and maintenance to reflect your unique situation accurately. Look for calculators that support different scenarios like lease vs. buy, cloud vs. on-premise, or single vs. multiple supplier quotes, giving you comprehensive insights into varying situations.
The output should include detailed cost-analysis reports and visual data representation, such as graphs or charts, for intuitive understanding. Ensure the calculator updates according to the latest economic and industry factors, offering accurate and relevant forecasts. This ability aids in predicting potential shifts in costs that might affect your business’s financial planning.
Feature | Description |
---|---|
Customization | Allows input of specific variables such as labor costs and energy usage. |
Scenario Analysis | Compares multiple financial models, such as lease or buy options. |
Visual Reporting | Generates graphs and charts for easier interpretation of data. |
Regular Updates | Ensures forecasts account for recent economic changes. |
Evaluate TCO calculators based on these criteria to select a tool that aligns with your business goals. By accurately estimating the TCO, businesses can optimize their investment strategies and minimize unforeseen expenses. An informed choice can drive significant financial efficiency and strategic advantage.
Understanding Total Cost of Ownership in Equipment Management
The initial purchase price is just a fraction of the true expense of owning equipment. To achieve accurate budgeting, consider all aspects of the total cost of ownership (TCO). Equipment management thrives when potential hidden costs are recognized early in the planning phase. Adopting a TCO perspective involves examining acquisition costs, maintenance expenses, operational efficiency, and eventual disposal values.
Focus on Maintenance: Regular maintenance costs can surpass the initial purchase price over the lifespan of equipment. Preventive maintenance minimizes downtime, extends machinery life, and reduces unexpected repairs. Allocate a budget for scheduled services, staff training, and spare parts.
Energy Consumption Matters: Energy usage significantly impacts TCO. Invest in energy-efficient models to ensure long-term savings. Analyze energy consumption data and perform audits to identify areas where efficiency improvements can be made.
Operational Efficiency: Downtime and productivity losses affect overall costs. Choose equipment that integrates seamlessly with your operations. Evaluate the ease of use, compatibility, and the required skill level of operators to maintain productivity.
Consider Depreciation and Resale Value: Depreciation affects asset value over time. A well-maintained piece of equipment can command a higher resale price. Keep detailed records and perform regular assessments to gauge when replacement might be economically viable.
Utilizing a total-cost-of-ownership calculator provides clear insights and aids in effective decision-making. A spreadsheet or specialized software can offer personalized cost assessments tailored to specific equipment classes. Strategic planning and informed investment decisions lead to optimal equipment management and cost savings over time.
Key Features to Look for in a TCO Calculator
Ensure the TCO calculator you choose offers a user-friendly interface that simplifies data entry and analysis. This feature minimizes errors and allows users to focus on drawing insights rather than struggling with complex inputs.
- Comprehensive Cost Analysis: The tool should account for acquisition, operational, and hidden costs–such as maintenance, energy consumption, and end-of-life costs–to give a complete picture of the total expenditure.
- Scalability: A good TCO calculator needs to handle different project sizes, from small-scale initiatives to large enterprise implementations, adapting to various business needs without sacrificing accuracy.
- Scenario Analysis: Look for the ability to model different scenarios by adjusting variables to see how changes affect total ownership costs. Scenario planning helps anticipate outcomes and supports better decision-making.
- Data Export Options: The ability to export data and results in various formats such as CSV or PDF is crucial for reporting and sharing insights with stakeholders or for further analysis.
- Integration Capabilities: Ensure the calculator can integrate with existing systems or software, such as accounting or ERP systems, for seamless data import and export, which enhances workflow efficiency.
- Regular Updates: The tool should receive frequent updates to accommodate new cost factors or changes in economic conditions, ensuring it remains relevant and accurate over time.
- Customizable Input Parameters: Allow users to tailor the input fields to fit unique business contexts, thereby increasing the precision of the calculations and results.
Invest in a TCO calculator that excels in these areas to maximize insight and strategic value from your cost assessments.
Comparing Different TCO Calculators: Pros and Cons
Choose a TCO calculator based on the specific needs of your project. There are different types available, each offering unique advantages and limitations. Here’s a breakdown to help you make an informed decision:
Spreadsheet-Based Calculators offer flexibility in data entry and analysis. Users can customize formulas and layouts. They provide a straightforward interface if you’re comfortable with spreadsheets, but they require manual effort to update and might introduce errors through accidental data modification.
Web-Based Calculators are accessible from any device with an internet connection, ensuring up-to-date features and data. They often integrate with cloud services for data storage and collaboration. However, they might restrict customization compared to spreadsheets and depend on your internet connectivity.
Software Applications provide automation, reducing manual input errors and offering integrated features like reporting and analysis tools. They usually have high initial setup costs and require training, but they streamline processes for larger organizations.
Industry-Specific Tools cater to particular sectors, offering tailored metrics and relevant benchmarks. They provide precision for specialized fields, but may lack versatility for broader applications.
While selecting a tool, balance your need for customization against ease of use and error-proofing. A small business might benefit more from a flexible spreadsheet model, while a larger company might find web-based or software solutions more suitable due to their automation capabilities.
Common Challenges Using TCO Calculators and How to Overcome Them
Begin by ensuring accurate data input. Inaccurate or incomplete data is the most common source of misleading results. Verify each data point for relevance and precision, including acquisition costs, ongoing maintenance, and operational expenses. Double-check figures and keep a record of data sources for future reference.
Another frequent issue is misunderstanding the scope of calculations. Clearly define what your TCO calculation will include and exclude. Consider all direct and indirect costs over the total lifecycle of the asset. Common omissions like software updates, training, and energy consumption can lead to underestimating the true cost.
Complex models and templates can overwhelm users. Simplify by breaking down inputs into manageable sections or steps. Use intuitive, user-friendly software that offers guidance throughout the process. This makes the calculator more accessible, even for those with less financial expertise.
Address the variability of future costs, which can be challenging to project. Use historical data and industry benchmarks to estimate future expenses. Implement a range of scenarios including best-case, worst-case, and most likely to accommodate uncertainty in these projections.
Lastly, there’s a challenge in aligning TCO results with strategic business goals. Always interpret the results within the broader context of your company’s objectives. Discuss findings with stakeholders, ensuring they understand the implications of TCO on decision-making and resource allocation. This collaborative approach can lead to more informed, strategic decisions.
Enhancing Decision-Making with TCO Calculators
Maximize the accuracy of your investment decisions by leveraging Total-Cost-of-Ownership (TCO) calculators. Begin by collecting relevant data concerning all possible costs associated with the acquisition, operation, and maintenance of an asset. This includes initial purchase price, operational expenses, maintenance, and potential resale value. Input this data into the TCO calculator to generate a comprehensive cost analysis.
Prioritize detailed data. Accurate inputs will yield reliable outputs, enabling you to make informed decisions aligned with your financial goals. Break down expenses into fixed and variable costs to provide clarity and support strategic planning.
Use the generated insights to compare different asset options. TCO calculators allow you to evaluate not just upfront costs but the long-term economic impact of your choices. This holistic approach enables prioritization of options that promise optimal cost efficiency over time.
Enhance strategic planning by incorporating TCO calculations into your financial models. Regularly update calculations with actual expense data to refine projections and adjust strategies as necessary.
By focusing on TCO, you shift from a short-term perspective to a long-term strategic outlook. This empowers you to allocate resources dynamically, ensuring sustainable financial health and competitive advantage. With precise information, embrace opportunities that offer superior value and minimize financial risks.
How to Implement and Use a TCO Calculator for Equipment
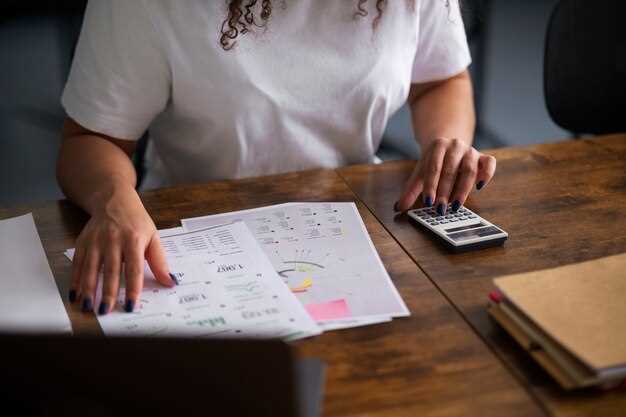
Selecting the right tools to calculate Total Cost of Ownership (TCO) for equipment is critical for making informed financial decisions. Begin by identifying your goals: are you evaluating a purchase decision, assessing current assets, or considering upgrades? Define the scope of what you wish to include in the TCO calculation.
- Choose a Suitable TCO Calculator: Ensure the calculator comprehensively accounts for all relevant costs, including purchase price, maintenance, operation, and downtime costs. Opt for one that provides customizable options to suit specific industry needs.
- Gather Accurate Data: Compile historical data on expenses such as purchase price, maintenance schedules, utility consumption, and lifetime expectancy. The more accurate your data, the more reliable the results.
- Customize Your Inputs: Adjust default values in the calculator to reflect real-world variables like usage frequency, operational hours, and local energy costs. This ensures a realistic projection of expenses.
- Analyze the Results: Use the calculator’s output to compare different scenarios, such as continuing with current equipment versus investing in new models. Focus on long-term cost savings rather than initial expenses.
- Revise Regularly: Update TCO calculations periodically with new data to reflect changing costs or operational conditions. This practice helps in adjusting strategies based on updated insights.
Employing a structured approach enables better budget allocation and financial planning. By systematically analyzing TCO, you can optimize asset management and make sound investment decisions.
Step-by-Step Guide to Downloading a TCO Calculator
Begin by identifying a reputable source for downloading your TCO Calculator. Visit the official website of a well-known provider in the field of cost analysis.
Locate the download section or search for “TCO Calculator” using the website’s search function. Typically, this can be found under resources, tools, or a similar heading.
Ensure that the calculator version you are selecting is compatible with your operating system. Compatibility information is often listed next to the download link.
Click the download link. Your browser might prompt you to choose a destination folder for the file; select a folder where you can easily locate the download.
Wait for the download to complete. Duration will vary depending on your internet speed.
Once the download is finished, navigate to the folder where the file was saved. Double-click the downloaded file to initiate the installation process.
Follow the on-screen installation instructions carefully. Typically, this includes agreeing to terms of service and choosing an installation path.
Complete the installation by clicking ‘Finish.’ Ensure that the program is accessible from your applications or desktop, confirming successful installation.
Launch the TCO Calculator to ensure it is working correctly. Check for any available software updates to keep the calculator running smoothly.
Setting Up the TCO Calculator for Your Equipment Needs
Identify the specific pieces of equipment you plan to assess. Create a detailed list, including item names, models, and any unique identifiers, to ensure you have all necessary information at your fingertips. Once you have this list, begin by gathering data on the initial purchase costs, as well as any financing details if applicable.
Next, focus on the operational costs. Include energy consumption, maintenance, repair costs, and any recurring fees associated with each piece of equipment. Be thorough, as these factors are crucial for an accurate total cost of ownership analysis. If possible, consult historical data or industry benchmarks for a more precise estimation.
Consider the lifespan of each item. Reliable estimates can often be sourced from manufacturer specifications or through industry research. This will allow you to distribute the costs over the projected lifespan accurately, which is key in determining long-term value.
Input the collected data into the TCO calculator, ensuring each field is filled accurately. Take advantage of any built-in features the calculator may offer, such as templates or examples, to verify the correctness of your entries.
After entering all relevant data, review the results to ensure they match expectations. Use this output to compare different equipment options side by side, aiding in strategic decision-making. Adjust parameters if necessary to model different scenarios, such as changes in usage patterns or potential maintenance expenses. This flexibility can provide deeper insights, helping you make informed, cost-effective choices for your equipment needs.
Interpreting Results to Optimize Ownership Costs
Analyze your highest cost drivers first to identify potential savings. Break down the total ownership costs into individual components like acquisition, operation, maintenance, and disposal costs. This separation allows you to pinpoint where most of your budget is being allocated and which parts can be streamlined.
Focus on reducing operational expenses through efficient resource management. For instance, energy-efficient equipment may have a higher upfront cost but can lead to substantial savings over its lifetime. Calculate the potential savings from reduced energy usage to determine the payback period.
Consider extending the lifespan of your assets through regular maintenance. Although it might seem like an extra expense, preventive maintenance can prevent costly repairs or early replacements, ultimately reducing the total cost over time.
Explore leasing or financing options if the initial acquisition cost is straining your budget. These alternatives can spread out expenses and preserve cash flow without significantly affecting long-term costs.
Evaluate the impact of indirect costs, such as training and downtime. Optimizing training procedures or minimizing downtime through operational improvements can decrease overall expenditures significantly.
Perform scenario analysis to understand how changes in different variables affect total costs. Modifying one element, such as supplier costs or operational efficiency, can illustrate potential outcomes and guide decision-making in cost management strategies.
Regularly review and update your cost assumptions to ensure they reflect current market conditions. This practice helps maintain an accurate picture of ownership costs and identifies new opportunities for optimization.
Q&A:
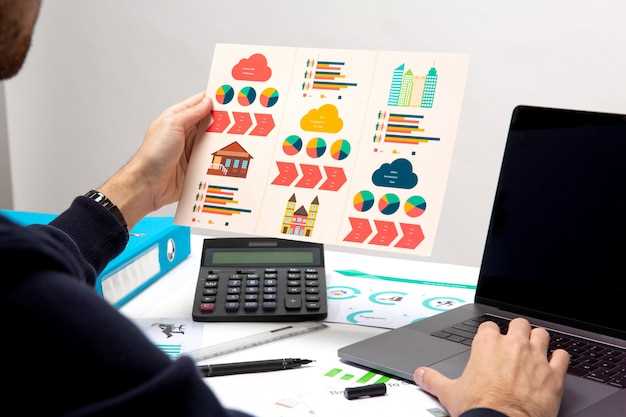
What is a Total-Cost-of-Ownership (TCO) Calculator, and why is it useful?
A Total-Cost-of-Ownership (TCO) Calculator is a tool that helps users estimate the cumulative cost of owning a product or service over its entire life cycle. It includes direct and indirect costs such as purchase price, maintenance, operating expenses, and more. This is useful for making informed financial decisions by revealing the actual expense beyond the initial purchase.
How can I download the TCO Calculator mentioned in the article?
To download the TCO Calculator, look for the download link provided in the article. Usually, such tools are available in formats like XLSX or online applications. Ensure you have the necessary software, such as Microsoft Excel, to open and use the file.
Does the article provide a step-by-step tutorial on using the TCO Calculator?
Yes, the article includes a detailed tutorial on how to use the TCO Calculator. It covers everything from initial setup to inputting data and interpreting the results, ensuring users can make the most out of the tool even if they are not familiar with cost analysis techniques.
Can this calculator be customized for different industries?
The TCO Calculator typically allows customization to suit various industries by providing templates or fields that can be adjusted according to specific needs and cost factors relevant to the industry in question, such as manufacturing, IT, or transportation.
Are there any limitations to using a TCO Calculator as mentioned in the article?
While a TCO Calculator is a valuable tool, it might not capture all cost variables or predict future changes that could affect overall expenses, such as inflation or technological advancements. Therefore, it is important to use this tool as part of a broader strategic assessment.
What factors does the Total-Cost-of-Ownership Calculator consider?
The Total-Cost-of-Ownership Calculator typically includes various factors such as initial purchase cost, maintenance expenses, operational costs, energy usage, and potential resale value. It aims to provide a comprehensive view of the total financial impact of owning a particular product over its lifecycle. By including these elements, users can make informed decisions and evaluate the long-term economic benefits or drawbacks.