Establishing a systematic preventive-maintenance schedule for your homogenizer significantly boosts its efficiency and longevity. Regular inspections and timely interventions are your best allies in minimizing unplanned downtimes. Begin by categorizing maintenance tasks into daily, weekly, and monthly routines, ensuring each aspect of the equipment is addressed systematically. This strategic approach not only aids in maintaining operational continuity but also enhances the overall quality of the output.
A crucial component of maintenance involves inspecting the homogenization system’s critical parts, including seals, valves, and pistons. Routine checks can unveil signs of wear and tear early, preventing extensive damage that often results in costly replacements. Utilize manufacturer-guided inspection procedures to ensure thoroughness and precision. Clearly documenting each maintenance activity provides valuable insights for future reference, assisting in predictive analytics and trend tracking.
Incorporating calibration checks into your maintenance schedule ensures that the homogenizer functions optimally within the specified parameters. Calibration not only maintains product consistency but also optimizes energy usage, resulting in notable cost savings. Establish a feedback mechanism with operators to quickly address any irregularities observed during operation. This continuous feedback loop fosters an environment of proactive maintenance, ultimately contributing to the machine’s robust performance.
Determining Optimal Inspection Frequencies for Homogenizers
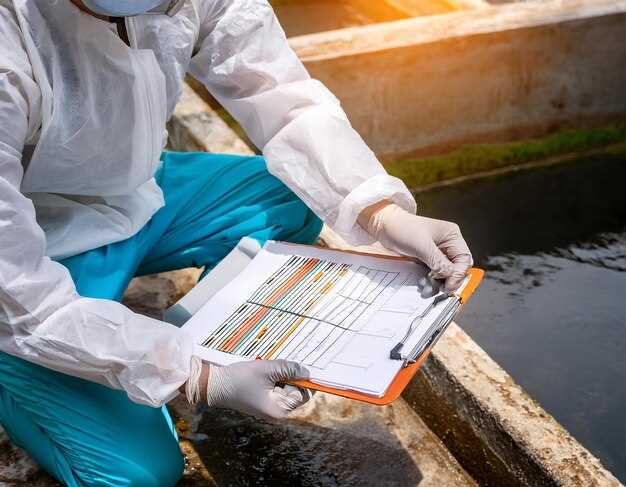
Schedule homogenizer inspections based on operation hours and environmental conditions. For systems operating under constant high-load conditions, inspect every 500 hours. For moderate use, a 1000-hour interval is suitable. Prioritize visual inspections weekly to spot wear and leaks early. Environmental factors like temperature and humidity significantly affect frequency. In harsher environments, consider bi-weekly checks. Keep detailed logs of previous maintenance and breakdowns to fine-tune schedules. This proactive approach minimizes downtime and extends equipment life.
Key Components Requiring Regular Maintenance
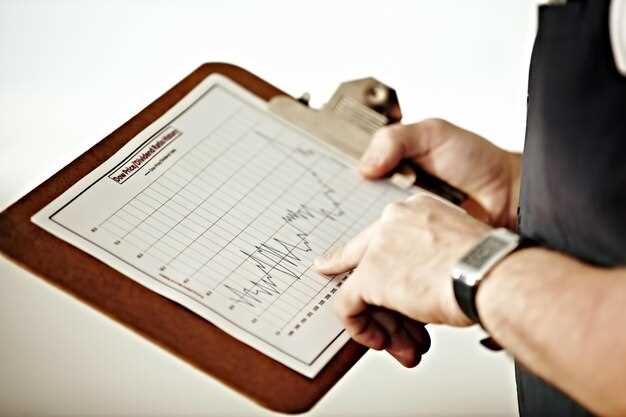
Prioritize the lubrication of bearings as improper lubrication leads to overheating and premature wear. Use manufacturer-recommended lubricants and schedules to prevent breakdowns. Inspect seals for any signs of wear, tears, or leaks, as damaged seals can lead to contamination and reduced efficiency.
Check the homogenizer’s valves and seats regularly for wear and tear. Replace them once you notice deformation to prevent exposure to uneven pressure which can affect performance. Monitor pressure gauges to ensure accurate readings, as inaccurate gauges can lead to operational errors.
Pipelines and connections should also be thoroughly inspected for leaks or blockages. Clear any debris to maintain smooth operation. Examine all safety devices, ensuring they function properly to prevent accidents. Perform calibration checks on all control instruments to maintain precision.
Component | Maintenance Action | Frequency |
---|---|---|
Bearings | Lubricate | Monthly |
Seals | Inspect & Replace if Necessary | Quarterly |
Valves & Seats | Inspect & Replace if Necessary | Biannually |
Pressure Gauges | Calibrate | Annually |
Pipelines & Connections | Inspect for Leaks/Blockages | Quarterly |
Safety Devices | Test Functionality | Biannually |
Thorough maintenance not only extends the life of a homogenizer but also ensures smooth operation and maximum efficiency. Allocate responsibilities to trained personnel for each component, fostering accountability and expertise in maintenance practices.
Developing a Checklist for Routine Homogenizer Maintenance
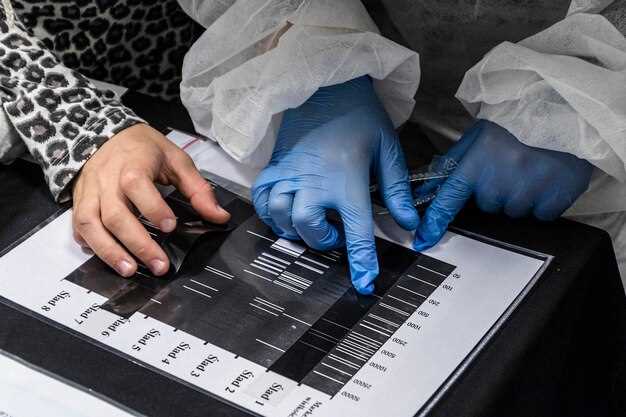
Identify key maintenance tasks to ensure efficient homogenizer operation and minimize downtime. Prioritize the following elements to create a comprehensive checklist:
- Inspect Seals and Gaskets: Check for wear and tear regularly. Replace immediately to prevent leaks and maintain pressure integrity.
- Monitor Motor Performance: Evaluate motor efficiency by measuring amperage draw. Variations may indicate underlying issues.
- Lubricate Bearings: Apply appropriate lubricant to bearings every month. Proper lubrication reduces friction and prevents overheating.
- Check for Vibration & Noise: Listen for unusual sounds which can signal component misalignment or wear.
- Clean Filters: Change filters as per manufacturer recommendations to ensure optimal performance and prevent contamination.
- Inspect Pressure Gauges: Verify the accuracy of pressure readings. Calibrate gauges regularly for precision.
- Examine Hoses & Connections: Ensure that all connections are secure and hoses are intact. Replace any damaged parts immediately.
- Assess Homogenizing Valve: Look for signs of erosion or damage. Regularly check alignment and replace parts as needed to maintain efficiency.
- Test Safety Devices: Regularly test pressure relief valves and other safety mechanisms to ensure dependability.
- Review Documentation: Maintain a detailed log of maintenance activities, including parts replaced and inspections performed.
Implementing this checklist facilitates proactive maintenance, reducing unexpected failures and extending the life of your homogenizer.
Documenting and Analyzing Maintenance Activities
Implement a structured documentation process for all homogenizer maintenance activities to improve efficiency and equipment lifespan. Begin by using standardized forms and digital tools to record every service event, component replaced, and issue resolved. This data forms the foundation for identifying recurring problems and areas for improvement.
Analyze maintenance logs regularly to uncover patterns in equipment failures and performance fluctuations. Apply predictive analytics to anticipate potential breakdowns, allowing for preemptive measures that minimize downtime. Share findings with the maintenance team through regular meetings to ensure continuous improvement and knowledge sharing.
Incorporate detailed metrics such as mean time between failures (MTBF) and mean time to repair (MTTR) into your analysis. These metrics provide insight into equipment reliability and efficiency, guiding decisions on maintenance frequency and methods. Establish clear benchmarks and objectives to gauge the success of maintenance activities.
Leverage automated systems and sensors on homogenizers for real-time monitoring, ensuring timely and accurate data collection. This approach not only streamlines the documentation process but also enhances the precision of analysis, leading to more informed maintenance strategies.
Strategies for Downtime Reduction in Homogenizer Operations
Consistently monitor the condition of key components such as seals, valves, and pistons to identify wear before it leads to failure. By implementing a predictive maintenance system, you can analyze operational data to forecast when parts are likely to require attention, which minimizes unscheduled interruptions.
Standardize the cleaning and sanitation schedules of homogenizers. Adhering to predefined procedures ensures that residue buildup is minimized, reducing strain on mechanical parts and enhancing operational efficiency.
Train your staff thoroughly to operate the equipment optimally. Well-informed operators can significantly extend the service life of machinery by ensuring proper usage and promptly addressing early signs of malfunction.
Utilize high-quality replacement parts from trusted suppliers to maintain performance standards. Inferior components often lead to increased failure rates and more frequent maintenance, disrupting production timelines.
Work closely with equipment manufacturers to schedule periodic reviews of operating protocols. Manufacturer insights can lead to adjustments or upgrades that align machinery performance with the latest technological advancements, optimizing uptime potential.
Identifying Common Causes of Unplanned Downtime
Implement regular training sessions for operators to ensure they understand the intricacies of the homogenizer, as operator error often leads to unexpected stoppages. Focus on detailed instruction regarding machine loading limits and routine checks, which helps in reducing strain and potential malfunctions.
Conduct periodic inspections of wear parts such as valves, seals, and homogenizing assemblies since normal wear and tear can escalate into significant breakdowns if neglected. Replace these components as needed to prevent failures during operation.
Address lubrication issues proactively by maintaining accurate records of lubricant levels and consistency checks. Inadequate lubrication is a frequent precursor to equipment overheating and subsequent downtime.
Upgrade software and firmware regularly to mitigate risks associated with outdated technology, which can cause system glitches or integration problems with newer equipment components. Ensure compatibility with existing machinery to avoid unexpected disruptions.
Deploy a robust monitoring system to track machine performance in real-time. This approach allows for immediate detection of anomalies such as pressure drops or temperature spikes, facilitating prompt corrective actions before they escalate into major issues.
Review and refine maintenance schedules based on historical data analysis to align with the actual rate of wear and tear observed. Adjusting frequency and scope can significantly reduce the unpredictability of mechanical failures.
Implementing Real-Time Monitoring Systems
Start by integrating sensors on critical components of your homogenizer. This provides continuous data on key parameters like pressure, temperature, and vibration levels. Download software that pairs with these sensors, offering instant data translation into actionable insights.
Create alerts for parameters that exceed normal ranges. This immediate feedback allows technicians to address issues before they escalate. Schedule maintenance tasks based on data trends rather than fixed intervals. This not only saves time but also minimizes wear and downtime.
Train staff to interpret data effectively. Host regular workshops to update your team on the latest software features and techniques. Encourage collaboration between departments to enhance operational efficiency through shared insights and strategies.
Invest in cloud-based solutions for data storage. This facilitates access from multiple devices, enabling remote monitoring and decision-making. Utilize analytics to spot long-term trends and predict potential failures, optimizing maintenance planning.
By embracing these strategies, you ensure that your homogenizer operates at peak performance with minimal disruption. Implement real-time monitoring to transition from reactive to proactive maintenance, enhancing overall productivity and reliability.
Trained Personnel: Importance of Skill Development and Training
Ensure your team receives regular training sessions focused on both theoretical knowledge and hands-on practice. Skilled personnel can identify wear and tear in homogenizers early, preventing costly breakdowns. Encourage technicians to attend workshops and certification courses that update their knowledge of the latest maintenance techniques. Properly trained staff can efficiently handle unexpected equipment malfunctions, reducing downtime.
Focus on interactive training modules that simulate real-world scenarios. Interactive training helps students grasp complex concepts faster and improves retention. Allocate resources for online courses and in-house sessions led by experienced engineers. Employees with comprehensive training can also contribute to optimizing maintenance schedules, increasing operational efficiency.
Incorporate cross-training practices to enable team members to understand various equipment types. Cross-training ensures that operations continue smoothly even when specific employees are unavailable. Foster a culture of continuous learning within your organization to enhance adaptability and innovation. This forward-thinking approach empowers employees to exceed maintenance standards and contribute to the longevity of your equipment.
Spare Parts Management for Homogenizers
Ensure consistent homogenizer performance by maintaining a well-organized spare parts inventory. Begin by creating a detailed list of all essential components including seals, valves, and gaskets. This allows quick access during routine checks or unexpected repairs.
Develop a tracking system using software that records parts usage and reorder times, minimizing the risk of downtime due to stock shortages. Set reorder points based on historical machine performance and part lifecycle data. This proactive approach helps maintain adequate stock levels without overstocking.
Conduct regular audits of your spare parts inventory to verify quantity and condition. Replace any parts showing signs of wear, even if not immediately required for maintenance. Consistent audits prevent future failures that could lead to costly downtime.
Collaborate with homogenizer manufacturers or authorized distributors for sourcing high-quality parts. Establishing relationships with reliable suppliers ensures access to genuine parts and potentially negotiated pricing, improving cost efficiency in the long run.
Implement staff training sessions to educate maintenance personnel on the importance of precise spare parts management. Proper handling and storing techniques extend part longevity and reduce unnecessary expenses.
By integrating these strategies into your maintenance schedule, you will sustain homogenizer efficiency, reduce unexpected breakdowns, and optimize overall operation costs.
Case Studies on Successful Downtime Reduction
Implement routine visual inspections to spot wear and tear early. XYZ Dairy improved equipment uptime by 20% after technicians began monthly visual checks on their homogenizers. Minor issues, like seal or gasket wear, were identified earlier, preventing larger mechanical failures.
- Proactive Parts Replacement: ABC Foods shifted from reactive repairs to scheduled parts replacement, reducing downtime by 30%. They determined key components, such as valves and pistons, prone to failure after certain operating hours and preemptively replaced them during scheduled maintenance.
- Advanced Lubrication Techniques: DEF Beverages utilized high-performance lubricants, applied systematically every quarter. This strategy extended component lifespan and fostered smoother operations, resulting in a 15% decrease in unscheduled stops.
- Cross-Training Staff: GHI Industries empowered their workforce by cross-training operators in basic maintenance tasks. With this approach, operators could immediately address minor issues, leading to a swift 25% reduction in overall downtime.
Analyze data from IoT devices to predict failures. JKL Processing saw real benefits by implementing IoT sensors that continuously monitor vibration and temperature. Real-time data analytics allowed them to foresee failures and plan maintenance during non-peak hours, trimming unexpected downtime by 40%.
- Utilize Predictive Analytics: A tool for downtime reduction, MNO Enterprises harnessed predictive analytics, using historical and real-time data to anticipate issues. Moving to this model slashed reactive maintenance by 35%.
- Regular Training and Updates: Updating employees on the latest maintenance techniques ensured a quick response to potential downtimes, as evidenced by PQR Firm, which noted a 22% fall in disruptions.
Adjust maintenance schedules based on equipment usage rather than a fixed calendar. STU Factory employed usage-driven scheduling, achieving a significant increase in uptime of 18% by aligning maintenance needs with actual workload.
Q&A:
Why is it important to follow a preventive maintenance schedule for a homogenizer?
Adhering to a preventive maintenance schedule for a homogenizer helps ensure optimal performance and prolongs the equipment’s lifespan. Regular maintenance can prevent unexpected breakdowns, minimize downtime, and ultimately save costs associated with extensive repairs. Moreover, it helps maintain the quality and consistency of the products processed using the homogenizer.
What are the key components of a homogenizer that need regular inspection during preventive maintenance?
The critical components that require regular inspection during preventive maintenance include the seals, valves, pistons, and homogenizing valves. These parts are subject to wear and tear due to constant usage and high pressures involved in the homogenizing process. Inspecting and, if necessary, replacing these components can prevent leaks and maintain efficient operation.
How frequently should preventive maintenance be conducted on a homogenizer?
The frequency of preventive maintenance for a homogenizer largely depends on the model and usage intensity. Typically, manufacturers provide maintenance schedules in their manuals, which may suggest routine checks weekly, monthly, or quarterly. It’s also advisable to consider additional checks if the equipment is used extensively or under strenuous conditions.
What are some common signs that a homogenizer might need maintenance outside of its regular schedule?
Common signs that a homogenizer may need maintenance outside its regular schedule include unusual noises during operation, decreased homogenization efficiency, visible leaks, and inconsistent product quality. If operators notice any of these symptoms, it is wise to conduct a thorough inspection and address any issues immediately to prevent further damage.
Can preventive maintenance improve the energy efficiency of a homogenizer?
Yes, preventive maintenance can enhance the energy efficiency of a homogenizer. Well-maintained machines run more smoothly and require less energy to operate efficiently. Addressing issues like worn-out parts or misalignments ensures that the homogenizer functions without expending excess power, leading to energy savings over time.