For industries seeking to optimize energy consumption, membrane filtration often emerges as the cost-effective choice. This technology harnesses pressure instead of heat, dramatically reducing energy usage. The specific energy requirement of membrane filtration can be as low as 1-5 kWh per cubic meter of treated liquid, especially in processes like reverse osmosis and ultrafiltration. By comparison, evaporation can demand 10-40 times more energy, primarily due to the heating required to vaporize liquids. This stark contrast makes membrane filtration highly appealing for cost-sensitive operations.
Membrane filtration not only conserves energy but also supports high operational efficiency. Its ability to selectively separate compounds without phase change significantly reduces energy loss. This advantage positions it as a sustainable choice for industries dealing with temperature-sensitive materials. The maintenance and operational costs are also lower, further enhancing its attractiveness.
While evaporation techniques have their place, especially when dealing with heat-tolerant substances, the energy implications can be substantial. The investment in insulation and heat recovery systems to mitigate energy inputs increases capital and maintenance costs. In sectors where lower energy consumption is paramount, membrane filtration provides a pragmatic solution.
Energy Consumption in Membrane Filtration
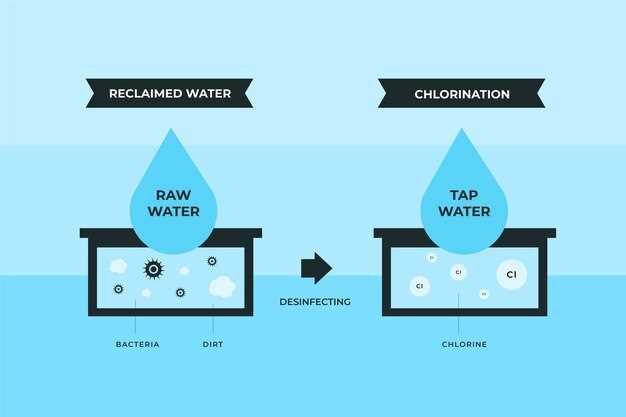
Prioritize choosing energy-efficient membrane systems by focusing on pressure requirements. High-pressure systems often consume more energy compared to low-pressure alternatives. Aim for membranes that operate effectively under lower pressures to reduce energy costs.
Consider the type of membrane. Nano-filtration and reverse osmosis are generally more energy-intensive than microfiltration due to the tighter pore structures that require higher pressures. Opt for microfiltration when dealing with larger particles or less stringent purity standards to conserve energy.
Regular maintenance of membrane modules significantly minimizes energy usage. Fouling or scaling can increase resistance, necessitating higher pressures to maintain flow rates. Implement routine cleaning schedules and monitor filtration performance to maintain optimal energy consumption.
Integrate energy recovery devices when applicable. Pressure exchangers or energy recovery turbines can recapture energy from the process, lowering overall consumption. Assess specific applications for potential integration to enhance system efficiency.
Investigate advancements in membrane materials and technologies. Research consistently introduces new materials with improved permeability and fouling resistance, offering energy-saving benefits. Stay updated with these developments to exploit potential reductions in energy demand.
Automate system controls to optimize operations based on real-time data. Adaptive systems can adjust pressure and flow rates to match varying process conditions, ensuring energy is used judiciously without compromising performance.
Collaborate with specialists to conduct energy audits of existing membrane filtration systems. These evaluations can reveal inefficiencies and suggest targeted improvements, focusing on enhancing energy efficiency while maintaining or enhancing output quality.
Technological Advancements in Membrane Filtration
Adopt nanostructured membranes to leverage their increased permeability and selectivity. These innovations have led to remarkable reductions in energy consumption, enhancing the practicality of water treatment and other filtration processes. Optimized module designs have contributed significantly by minimizing hydraulic resistance and maximizing surface area, which boosts overall performance.
Invest in intelligent membrane monitoring systems that utilize sensors and AI algorithms to predict maintenance needs and optimize operational parameters. These systems reduce downtime and extend membrane life, adding cost efficiency across the board. Surface modifications further enhance membrane functionality; coatings that resist fouling drastically minimize the need for chemical cleaning, preserving the integrity of the filtration process while lowering operational costs.
Explore bioinspired membrane technologies that mimic natural systems for improved efficiency and sustainability. These designs unlock new potentials in selectivity and permeability, making them ideal for complex filtration tasks. Stay abreast of advancements in graphene-oxide-based membranes, which offer exceptional water flux and selective separation capabilities. Embracing these technological innovations ensures a competitive edge in membrane filtration applications.
Power Requirements: Membrane Systems vs. Traditional Methods
Choose membrane filtration for energy savings and efficiency. Membrane systems typically require less energy due to lower operational pressures compared to evaporation methods. For instance, reverse osmosis, a common membrane filtration process, operates at pressures between 5 to 25 bar. In contrast, traditional thermal evaporation systems require considerable energy to heat large volumes of water to boiling point, potentially reaching energy consumption levels up to 10 times higher.
Reduce carbon footprints by integrating membrane technologies. The energy efficiency of membrane systems translates directly into reduced greenhouse gas emissions. Studies reveal that membrane processes, such as nanofiltration and ultrafiltration, consume about 0.5 to 6 kWh per cubic meter, compared to 15 to 200 kWh per cubic meter for conventional evaporation processes. This not only minimizes environmental impact but also offers economic advantages in industries sensitive to energy costs.
Optimize process flexibility using membranes. These systems allow for easy scaling and adjustments in response to varying capacities, without substantial changes to power infrastructure. This adaptability provides a significant edge over traditional evaporation systems, which often require extensive energy and infrastructure investments for scaling.
Invest in membrane technology to capitalize on maintenance benefits. Membrane systems generally demand lower maintenance compared to evaporation systems, which suffer from scaling and corrosion issues. Reducing downtimes and maintenance intervals further amplifies the energy efficiency, as membranes maintain operational effectiveness over extended periods with consistent low power requirements.
Cost Analysis: Energy Expenditure Over Time
Choose membrane filtration for a cost-effective energy solution over time. Data shows that while initial investment costs might be higher, energy consumption significantly reduces operational expenses. Research indicates that membrane filtration systems use substantially less energy than evaporation–up to 90% less in certain applications. This energy efficiency leads to lower costs, especially in operations requiring large volumes of liquid processing.
Assess the long-term energy expenses of both methods to make informed decisions. Comparing the energy expenditure over several years reveals that the total cost of ownership leans favorably towards membrane filtration.
Filtration Method | Initial Investment ($) | Annual Energy Cost ($) | 5-Year Energy Cost ($) |
---|---|---|---|
Membrane Filtration | 150,000 | 20,000 | 100,000 |
Evaporation | 100,000 | 60,000 | 300,000 |
Opt for membrane filtration to avoid the higher cumulative consumption associated with evaporation. Savings accumulate as systems operate with reduced energy input, leading to lower bills. Maintenance costs are also typically less, contributing further to long-term financial benefits. Consider these factors to optimize operational budgets effectively.
Environmental Impact of Energy Use in Membrane Processes
Optimize energy efficiency in membrane processes to significantly lower environmental footprints. Begin by selecting the most energy-efficient membrane technology tailored to the specific application. Technologies such as reverse osmosis generally require less energy compared to traditional thermal methods.
- Energy Consumption: Membrane processes, like nanofiltration, often consume less than 4 kWh/m³ depending on the membrane type and operational settings. This efficiency directly reduces carbon emissions compared to evaporation methods.
- Renewable Energy Integration: Prioritize integrating renewable energy sources such as solar or wind. Transitioning to renewables can minimize greenhouse gas contributions and align operations with sustainability goals.
- System Design Optimization: Implement energy recovery devices, such as pressure exchangers, to recuperate and reuse energy that would otherwise be wasted. This can reduce energy use by 20-30% in some cases.
- Water Source and Quality: Pre-treat feed water to remove particulates and organics, reducing membrane fouling and, consequently, energy consumption. This leads to less frequent cleaning and maintenance, conserving resources and energy.
- Lifecycle Assessment: Conduct comprehensive assessments to evaluate the total environmental impact, including the production and disposal of membranes. Opt for recyclable or longer-lasting materials to mitigate adverse ecological effects.
Continuously monitor and refine operations to achieve sustainable practices in membrane technology. Implementing these strategies not only curtails energy usage but also supports global efforts toward a cleaner, greener future.
Energy Benchmarking in Dairy Processing
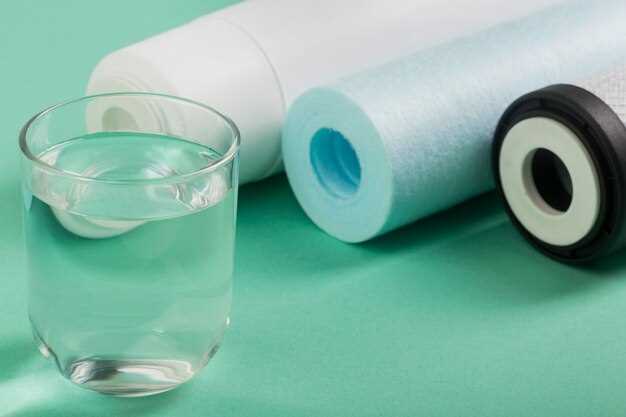
Prioritize implementing membrane filtration in dairy processing to significantly reduce energy consumption. It functions more efficiently than traditional evaporation methods and offers up to 85% energy savings. With typical energy costs comprising around 40% of total processing expenses, adopting energy-efficient technologies like membrane systems is a strategic move to improve profitability.
Invest in energy audits to identify areas for improvement in your current setup. This evaluation can reveal inefficiencies and opportunities for energy recovery. For instance, utilizing waste heat from one process to preheat another can result in considerable energy conservation.
Optimize process parameters such as pressure and flow rate in membrane operations to enhance energy efficiency. Fine-tuning these settings can reduce the energy footprint without compromising product quality. Regular maintenance ensures the systems operate at peak efficiency, preventing energy wastage.
Incorporate computerized monitoring systems to continuously track energy consumption and system performance. These systems provide real-time data and analytics, enabling quick adjustments and informed decision-making.
Train staff on the principles of energy-efficient practices and engage them in achieving energy-saving goals. Active participation of the workforce is key to sustaining long-term energy reduction achievements.
By embracing these strategies, dairy processors can lower energy costs, increase production sustainability, and maintain competitive market positioning.
Case Studies: Dairy Plants Implementing Membrane Filtration
Choose membrane filtration systems in dairy processing to significantly reduce energy consumption and improve efficiency. Dairy plants worldwide are embracing this technology to enhance productivity and sustainability. Below are specific cases where membrane filtration has made a noticeable impact.
- Dairy Plant in Denmark: This facility integrated ultrafiltration (UF) to concentrate milk proteins effectively, halving their energy consumption compared to traditional evaporation methods. By leveraging the lower thermal requirements of UF, the plant reduced its carbon footprint and improved operational costs.
- Australian Dairy Facility: Here, reverse osmosis (RO) replaced conventional methods for pre-concentrating milk. As a result, water recovery rates improved by 70%, and the energy usage dropped substantially, leading to yearly savings of up to 15% on electricity bills.
- US-Based Cheese Manufacturer: Implementing microfiltration (MF) allowed this plant to enhance cheese yield by up to 10% while slashing steam consumption by 30%. This change not only reduced energy usage but also elevated the quality of the final product by removing more bacteria from raw milk.
- French Yogurt Producer: Utilized nanofiltration (NF) to demineralize whey, resulting in a 20% energy reduction and an increase in product purity. The long-term efficiency gains made NF an appealing long-term investment, supporting both economic and environmental goals.
These examples illustrate the tangible benefits of membrane filtration in dairy production, offering a viable path towards sustainable and cost-effective operations. To capitalize on these advantages, plants should analyze specific production needs and select appropriate membrane technologies that align with their environmental and economic targets.
Comparative Analysis: Energy Efficiency of Membrane Filtration vs. Evaporation in Dairy
Membrane filtration provides a significant energy advantage over traditional evaporation methods in dairy processing. Research shows that membrane techniques, such as reverse osmosis and ultrafiltration, consume approximately 10% of the energy required by evaporation processes. This substantial reduction results from the lower thermal energy demands, as membranes operate under ambient conditions.
For every kilogram of water removed using evaporation, energy usage can exceed 500 kWh, while membrane filtration may require as little as 50 kWh. This difference highlights membrane technology’s efficiency, making it especially beneficial for energy-intensive operations. Furthermore, membrane systems offer enhanced flexibility in processing, enabling the selective concentration of proteins and other valuable components without sacrificing quality.
The transition to membrane filtration also supports sustainability goals through reduced carbon emissions. By minimizing reliance on steam and other heating mechanisms, the dairy industry can decrease its greenhouse gas footprint. Operators can further optimize energy consumption by integrating hybrid systems that combine initial membrane concentration with minimal subsequent evaporation.
Implementing membrane technology not only promotes energy savings but also reduces the overall cost of production, contributing to more competitive pricing in the dairy market. With advancements in membrane materials and configurations, industries can achieve even greater efficiencies, propelling this method as the preferred choice for modern dairy processing.
Optimizing Energy Use: Best Practices for Dairy Industry
Implement energy-efficient motors and pumps to immediately reduce energy consumption in dairy processing. Choose variable speed drives for pumps to match the operational demands more precisely, enabling energy savings of up to 30%. Ensure regular maintenance of all equipment to prevent energy losses due to inefficiency. Conduct periodic energy audits to identify potential improvements in existing systems.
Use heat recovery systems to reclaim energy from hot streams, such as pasteurizers and spray dryers. This recovered heat can be utilized in preheating processes, reducing the consumption of primary energy sources by 15-20%. Adopt membrane filtration methods like microfiltration or ultrafiltration; these require less energy compared to traditional evaporation techniques while maintaining product quality. This not only reduces the thermal load but also the cooling requirements, cutting energy costs further.
Invest in energy management software to monitor and optimize energy consumption across the entire facility. These systems provide real-time data, allowing for adjustments that can lower energy usage by 10%. Encourage a culture of energy efficiency among employees through regular training, helping to identify areas of waste during daily operations.
Install LED lighting and automated switches in all facilities to minimize electricity use. Compared to traditional lighting, LEDs consume up to 75% less energy and have a significantly longer lifespan. Take advantage of off-peak electricity rates by scheduling energy-intensive processes during periods of lower demand.
Transition to renewable energy sources, such as biogas from dairy waste or solar panels, to supplement traditional energy needs. This not only reduces dependency on non-renewable energy but also aligns with environmental sustainability goals. Aim for continuous improvement by setting measurable energy-saving targets, evaluating progress regularly, and adapting strategies as needed.
Challenges and Solutions in Dairy Membrane Filtration
Faced with operational stability issues in dairy membrane filtration, consider investing in regular membrane cleaning schedules. Effective cleaning protocols significantly extend membrane lifespan and enhance performance.
Scaling and Fouling: Combat scaling and fouling by optimizing feed quality. Ensure proper pre-treatment of dairy feed streams, including adjusting pH and temperature. Employ anti-scalant chemicals judiciously to minimize deposition without harming membranes.
Energy Consumption: Target high energy usage by selecting low-pressure membrane systems. Prioritize systems with energy recovery devices, reducing operational costs while maintaining efficiency. Additionally, explore the latest energy-efficient filtration technologies that align with sustainable practices.
Membrane Material Limitations: Address limitations by exploring advanced composite materials resistant to biochemical reactions. These new materials offer improved durability and resistance to clogging.
Permeate Quality: Maintain high permeate quality by continuously monitoring membrane condition in real-time. Implement automated systems for predictive maintenance, effectively reducing risks of sudden performance drops.
Through these targeted strategies, dairy processes can overcome existing challenges, achieving maximum efficiency and high-quality outputs without compromise.
Q&A:
How does the energy consumption of membrane filtration compare to that of evaporation in industrial applications?
Membrane filtration generally consumes less energy than evaporation. Filtration uses a pressure-driven process to separate substances, whereas evaporation requires thermal energy to convert liquids into vapor. This makes membrane filtration more energy-efficient, especially in large-scale applications where reducing energy costs is a priority.
What are the primary factors that influence the choice between using membrane filtration and evaporation?
The decision often hinges on specific requirements such as energy consumption, operational costs, and the nature of the material being processed. Membrane filtration is preferable when minimizing energy use and maintaining the integrity of sensitive materials are critical. On the other hand, evaporation might be chosen when a higher degree of separation is necessary, despite higher energy requirements.
Are there any environmental impacts associated with using membrane filtration over evaporation?
Membrane filtration tends to have a lower environmental impact due to its reduced energy usage, resulting in decreased greenhouse gas emissions when compared to energy-intensive evaporation processes. Additionally, it doesn’t require chemical additives or high temperatures, making it a more sustainable choice in terms of operational footprint.
What innovations are being developed to make evaporation more energy-efficient?
Innovations like mechanical vapor recompression (MVR) and multiple-effect evaporation (MEE) are being integrated to enhance the energy efficiency of evaporation technologies. These methods recycle energy within the system, reducing overall consumption. Such advancements are promising in making evaporation a more sustainable option.
What industries benefit most from the use of membrane filtration over evaporation?
Industries such as food and beverage, pharmaceuticals, and water treatment benefit greatly from membrane filtration. This is due to its energy efficiency, ability to operate at lower temperatures, and capability to preserve the quality of delicate components in the processed materials.
What are the main energy differences between membrane filtration and evaporation?
The primary energy difference between membrane filtration and evaporation lies in their respective operational mechanisms. Membrane filtration relies on pressure to separate particles or solutes from a liquid, which typically requires less energy compared to the thermal energy needed for evaporation. Evaporation processes require substantial heat to vaporize the solvent, making it generally more energy-intensive. Factors such as the type of membrane, pressure levels used, and specific thermal requirements of the solvent in evaporation play significant roles in determining the actual energy consumption of each method. Therefore, while membrane filtration is generally more energy-efficient, specific conditions and technological implementations can affect the overall energy efficiency of these techniques.