Implement a dedicated heat exchanger stack to isolate heat from residual plant processes swiftly. This solution not only reclaims energy efficiently but also minimizes contamination risks between streams. A beverage plant often harbors various waste heat sources, such as condensers, exhausts, and pasteurizers. By targeting high-heat output areas primarily, the plant can significantly capitalize on available thermal energy, reducing boiler fuel consumption dramatically and cutting costs.
Adopt a modular heat recovery system to allow flexible scaling in response to production variances. By integrating such a system, beverage plants can adapt to fluctuating production demands seamlessly, ensuring optimized heat recovery regardless of output levels. This modularity promotes operational flexibility and facilitates maintenance by isolating components without halting overall plant functions.
To maximize efficiency, analyze the thermodynamic profile of each process stage and tune the recovery system to align with peak temperatures. Data-driven adjustments enhance recovery yields and prevent energy wastage. Prioritize retrofitting older equipment with advanced technology upgrades that offer better thermal capture, helping plants maintain a competitive edge in energy conservation.
Ensure rigorous staff training on operating heat recovery systems. Knowledgeable staff can make real-time adjustments to enhance system throughput, troubleshoot issues promptly, and identify potential enhancements proactively. Include regular seminars and workshops in the training regimen to keep personnel updated on the latest technologies and methodologies in waste-heat recovery.
Waste-Heat Recovery in Beverage Plants: Practical Insights
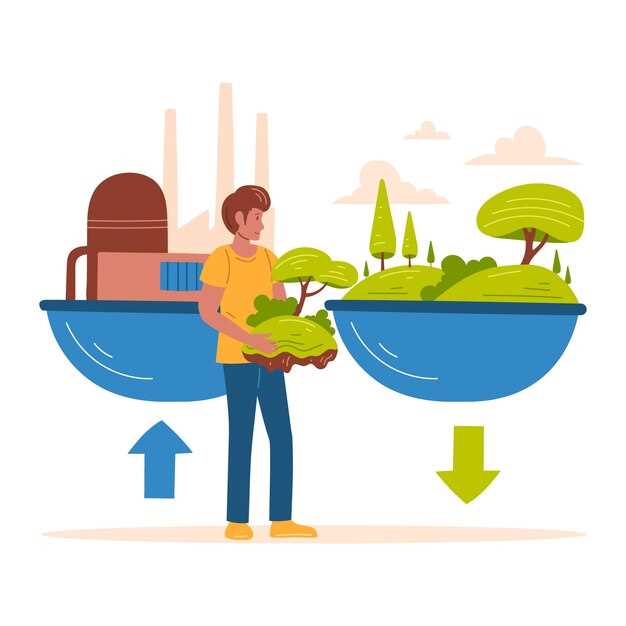
Consider harnessing the energy from the boiler blowdown processes to enhance your plant’s efficiency. This method involves heat exchangers that transfer energy from the high-temperature blowdown water to incoming cold feedwater. By preheating the feedwater, you can significantly reduce fuel consumption, leading to cost savings and lower emissions.
Regularly inspect and clean your heat exchangers to maintain optimal performance. Fouling can severely decrease efficiency, leading to diminished returns from your investment in waste-heat recovery infrastructure. Employ a preventative maintenance schedule to ensure equipment remains at peak performance.
Integration of a heat recovery steam generator (HRSG) behind your gas turbine can capture waste heat efficiently. This recovered heat can then be utilized in various plant operations, such as pasteurization or concentrating processes, further reducing operational costs.
Training operational staff on the nuances of waste-heat recovery systems is crucial in ensuring that all the equipment operates at maximum capacity. Comprehensive training programs will help staff members recognize inefficiencies early, preventing energy loss and unnecessary downtimes.
Use real-time monitoring systems to track and analyze heat recovery metrics. These systems provide valuable insights into energy usage patterns and help in identifying areas where further reductions can be achieved. Continuously optimize settings based on this data to sustain enhanced recovery performance.
Design Considerations for Waste-Heat Recovery Systems
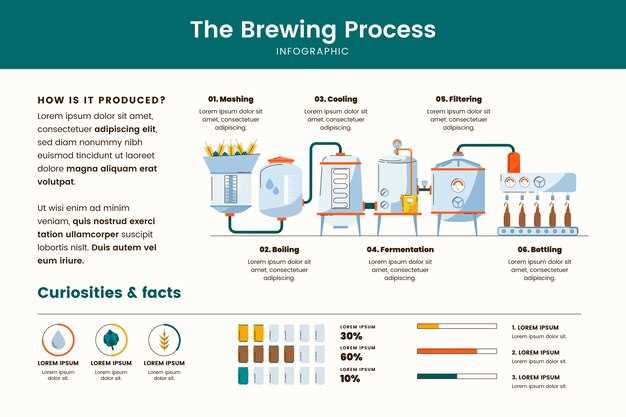
Prioritize accurate assessment of heat sources within your beverage plant. Identify and quantify heat loads from processes such as pasteurization, cooling, and distillation. Accurate data collection is crucial for choosing a system that meets your recovery needs without oversizing, which would lead to inefficiencies.
Incorporate the flexibility to handle variable production loads. Since beverage production can have fluctuating demand, your system should efficiently manage both peak and low operational periods. Implement control strategies like variable frequency drives to adjust recovery rates dynamically.
Focus on the integration with existing processes. Ensure the heat recovery system complements the plant’s infrastructure, minimizing downtime during installation. Look into modular systems that allow phased implementation. This approach reduces risk and provides the opportunity to evaluate benefits incrementally.
Choose materials that resist corrosion and fouling. The beverage industry often deals with processes involving acids and sugars, leading to equipment degradation. Use stainless steel and other corrosion-resistant materials to ensure longevity and reliability.
Evaluate the feasibility of multiple recovery technologies. Consider options like economizers, heat exchangers, and absorption chillers, and compare their efficiencies for your specific needs. Performing a cost-benefit analysis helps justify the investment and pinpoint the optimal technology mix.
Implement thorough monitoring and maintenance protocols. Install sensors to track system performance continuously and set up regular inspections to prevent potential failures. Proactive maintenance extends system life and sustains energy savings over time.
Finally, align your design with sustainability goals and regulatory requirements. By doing so, you ensure compliance while potentially benefiting from incentives aimed at reducing energy consumption and greenhouse gas emissions.
Assessing the Energy Profile of Beverage Plants
Evaluate power usage by installing smart meters throughout the facility. These meters provide real-time data, helping identify areas of excessive consumption. Prioritize high-energy zones such as refrigeration and pasteurization units. Use this information to devise strategies that optimize energy use.
- Analyze historical energy data to establish baseline consumption patterns. Identify peaks and off-peak hours to adjust operations for better efficiency.
- Conduct thermal imaging to detect heat loss in equipment and building structures. Implement insulation solutions where significant heat is dissipated.
- Measure the energy output of installed renewable systems, such as solar panels or biogas generators, to ensure their effectiveness in offsetting grid energy reliance.
- Monitor the performance of HVAC systems. Regular maintenance and upgrades can prevent unnecessary energy waste.
- Calculate the energy intensity of production processes, identifying areas where material and energy could be used more judiciously.
After gathering comprehensive data, set tangible energy reduction goals for the plant. Ensure ongoing monitoring to stay on track and adjust tactics as necessary. Engage plant personnel by educating them on energy-saving practices to create an inclusive sustainability culture.
Selecting Appropriate Heat Exchangers for Beverage Processes
Prioritize selecting a heat exchanger based on the specific type of beverage being processed. For carbonated drinks, tubular heat exchangers often perform best, as they handle the high viscosity and provide efficient heat transfer. Consider plate heat exchangers for juices, as they offer minimal fouling and easy maintenance, which is essential for high hygiene standards.
For plants dealing with large volumes, spiral heat exchangers may offer superior performance thanks to their compact design and efficient heat transfer capabilities, reducing energy consumption significantly. Mind the material used in the heat exchanger, opting for stainless steel when working with acidic beverages like citrus juices, to prevent corrosion and contamination.
Evaluate the required heat recovery rate and source temperature. The exchanger should seamlessly integrate with existing systems, minimizing disruptions and maximizing energy retention. Always account for cleaning-in-place (CIP) requirements to ensure minimal downtime, which is critical for maintaining productivity in continuous operations.
Budget constraints shouldn’t compromise quality. Efficient heat exchangers often result in substantial long-term savings by reducing energy costs and extending system longevity. Focus on total cost of ownership, including maintenance, instead of just initial acquisition costs.
Integration of Waste-Heat Recovery with Existing Infrastructure
Choose heat exchangers based on their compatibility with current steam and cooling systems. Evaluate the existing energy flow and identify areas where waste heat can be diverted efficiently. Prioritize systems that offer straightforward integration to minimize additional costs.
Ensure your control systems can handle increased data from recovered heat processes. Adjust the sensors and monitoring tools to track performance seamlessly, providing real-time feedback for any required adjustments. Invest in compatible upgrades for enhanced efficiency.
Review insulation of existing infrastructure to prevent heat loss. Collaborate with suppliers to select materials that bolster current insulation arrangements, thus maximizing retained temperature levels during heat recovery. Implement rigorous testing post-installation to validate improvements.
Leverage your current IT infrastructure to incorporate new software that facilitates process automation and monitoring. Utilize advanced analytics to interpret data from heat recovery initiatives, identifying opportunities for further optimization and predictive maintenance.
Engage cross-functional teams in training programs to ensure smooth adoption of new processes. Focus on fostering a culture of energy efficiency, encouraging staff to contribute ideas for optimization.
Identify potential for scaling projects by evaluating the feasibility of expanding recovery systems. Prioritize projects that offer the greatest return on investment and match your plant’s production goals. This strategic alignment ensures sustainable growth and enhanced energy efficiency.
Overcoming Space Constraints in Facility Layouts
Prioritize modular equipment selection to maximize flexibility in confined spaces. Opt for machinery with a compact footprint but high efficiency. For instance, choose vertical heat exchangers over horizontal models to save floor space. Implement a multifunctional equipment approach; equipment that serves dual purposes can substantially reduce spatial needs.
Integrate heat recovery systems directly into existing structures. Utilize rooftop spaces for auxiliary equipment, such as heat pumps. This approach minimizes on-ground disruption and effectively uses underutilized areas. When laying out piping, consider overhead installations to free up valuable floor area.
Adopt a digital layout planning tool to visualize and modify plant designs in real-time. These tools can highlight bottlenecks and test various configurations for optimal space use without physical rework. Additionally, maintain wide corridors for ease of movement, which facilitates efficient workflow while minimizing disruption risk.
Finally, implement a regular maintenance schedule to ensure that equipment operates at peak performance. This prevents unnecessary downtime and keeps equipment compact by avoiding the need for extra backup units. By following these strategies, plants can effectively manage space constraints while enhancing operational efficiency.
Economiser Retrofit: Enhancing Thermal Efficiency
Target the economiser area to bolster your plant’s thermal efficiency. Begin by assessing existing boiler systems to identify potential enhancements. An economiser retrofit can recuperate heat from flue gases, significantly improving energy usage. Consider these specific actions:
- Evaluate Flue Gas Temperature: Optimally, flue gases should be cooled to 120-150°C. If temperatures exceed this range, potential recovery opportunities exist.
- Select an Appropriate Economiser Type: Depending on the plant’s steam and heating requirements, choose between condensing and non-condensing economisers. Condensing types capture latent heat, offering higher efficiency for applications with low return water temperatures.
- Assess Material Compatibility: Ensure the economiser materials are corrosion-resistant to tolerate acidic condensates, especially when operating in condensing conditions.
- Calculate ROI and Payback Period: Conduct a thorough financial analysis considering installation costs, operational savings, and anticipated downtime, targeting payback within 3-5 years.
- Review Boiler Controls: Retrofit controls for better integration with the economiser, allowing automatic adjustments to maximize heat recovery.
- Implement Routine Maintenance: Regular inspections and cleaning protocols prevent fouling, ensuring optimal performance and longevity of the equipment.
By strategically retrofitting economisers, beverage plants can achieve notable reductions in energy consumption and emissions, aligning operations with sustainability goals and reducing operational costs.
Identifying Retrofit Opportunities in Existing Systems
Audit your existing heat recovery systems to pinpoint inefficiencies. Analyze energy flow using sub-metering to gather precise data. Focus on process areas with high heat loss, such as boilers and pasteurization units. Identify components that frequently operate below optimal temperature levels.
Implement a thermal imaging survey to visualize heat distribution and spot thermal leaks or inefficient heat exchangers. Prioritize areas where simple pipe insulation or valve upgrades can rapidly reduce thermal loss. Evaluate whether supplementing current systems with additional heat exchangers or condensate recovery systems can significantly improve efficiency.
Engage with maintenance teams to identify recurring issues with equipment that may signal high priority retrofit opportunities. Seek feedback from operators to understand manual workarounds impacting system performance. The goal is to create a proactive maintenance schedule that includes retrofit actions likely to yield swift energy savings.
Consider emerging technologies, such as predictive analytics, to anticipate heat recovery system failures before they occur. Monitor system parameters in real-time for anomaly detection and predictive maintenance alerts.
Opportunity | Action | Potential Impact |
---|---|---|
Thermal Leak Detection | Use thermal imaging surveys | Improve insulation, reduce energy waste |
Inefficient Heat Exchangers | Upgrade or replace exchangers | Boost heat recovery efficiency |
Condensate Recovery Enhancements | Add supplementary systems | Lower water and energy usage |
Data-Driven Maintenance | Implement predictive analytics | Reduce downtime and maintenance costs |
Prioritize retrofit projects based on potential energy savings and return on investment. Consult with energy consultants to explore incentive programs or rebates for energy-efficient upgrades. A strategic approach to retrofitting maximizes resource utilization and facilitates a more sustainable operation.
Compatibility of Economisers with Plant Operations
Ensure that the economiser is correctly integrated with the existing systems. A thorough energy audit will help identify where waste heat is available and how it can best be captured. When selecting an economiser, prioritize units that are flexible and can handle the variable load conditions typical in beverage plants. Look for models that allow for easy adjustments and maintenance without disrupting production schedules.
Choose materials that resist the corrosive properties of beverage byproducts. Stainless steel or coated surfaces often perform better, extending the lifespan of the economiser. Integrating sensors can facilitate real-time monitoring, ensuring that the system operates within optimal parameters and alerting staff to necessary maintenance before issues escalate.
Align the economiser’s capabilities with the plant’s thermal requirements. It should seamlessly channel recovered heat into pasteurization, cleaning processes, or heating incoming water. Properly sized economisers prevent energy wastage and maximize recovery, which leads to direct cost savings.
Coordinate with plant engineers to incorporate economiser control systems into existing plant management software. This integration allows for more precise temperature regulation and efficiency tracking. By fostering collaboration between operational staff and engineering teams, plants can ensure a smoother implementation and more effective use of economisers.
Conduct regular staff training sessions to calibrate and monitor economisers effectively, avoiding performance dips and costly downtimes. This ensures that the team remains adept at identifying and addressing potential issues swiftly. Furthermore, keeping personnel informed enhances operational harmony with the new system, reducing resistance to procedural changes.
Cost-Benefit Analysis for Economiser Installation
Install an economiser to significantly reduce energy costs by capturing waste heat from the boiler exhaust. Initial investments can be substantial; however, the payback period typically ranges from 1 to 3 years. Carefully evaluate the specific heat recovery potential, often between 10% to 20%, depending on boiler efficiency and operating conditions. This translates into considerable fuel savings, substantially lowering operational expenses.
Quantify potential savings by calculating the annual energy reduction. For instance, reducing fuel consumption by 15% in a plant with energy costs of $100,000 annually saves $15,000, highlighting the financial viability of the installation. Also, consider maintenance and operational costs. Modern economisers require minimal upkeep, further enhancing their return on investment.
Additionally, assess environmental benefits. Lower fuel consumption means reduced CO2 emissions, assisting in sustainability goals. This could open avenues for energy credits or incentives, which governments often provide for green initiatives, adding another layer of financial advantage.
Before deciding, conduct a detailed analysis considering plant-specific parameters and available economiser technologies. Consult with engineers to tailor solutions, optimizing for both performance and cost. Through this strategic approach, maximising the benefits while minimising risks becomes achievable, ensuring a smart financial move for the beverage plant.
Video:
How does waste-heat recovery work in beverage plants?
Waste-heat recovery in beverage plants involves capturing and reusing the excess heat produced during various production processes. This heat, which would otherwise be wasted, can be redirected to preheat water or other fluids, aiding in reducing the plant’s overall energy consumption and emissions.
What are the main design tips for implementing waste-heat recovery in beverage plants?
Some important design tips include assessing the current heat sources and understanding their variability, selecting the right heat exchangers, and integrating the recovery system seamlessly into existing plant operations. It’s crucial to match the recovered heat with the process needing energy, such as pasteurization or cleaning, to maximize efficiency.
What challenges might engineers face when designing a waste-heat recovery system for a beverage plant?
Engineers might encounter challenges such as space constraints for adding new equipment, dealing with variable heat loads, ensuring compatibility with existing systems, and managing the initial installation costs. It’s also important to maintain the food safety standards without compromising quality during the integration process.
Can waste-heat recovery significantly reduce operational costs in beverage plants?
Yes, waste-heat recovery can lead to noticeable reductions in operational costs by lowering energy demand from external sources. By utilizing excess heat that would otherwise be discarded, beverage plants can save money on heating and cooling, leading to improved profitability over time.
Are there specific examples or case studies showing successful implementation of waste-heat recovery in beverage plants?
Many beverage companies have successfully implemented waste-heat recovery systems. For instance, a brewery might use the captured heat to warm up water for brewing or cleaning processes. Case studies often highlight examples of energy savings, reduced carbon footprint, and compliance with sustainability goals, demonstrating the tangible benefits of such systems.